Wafer-dicingtechnology, as in krityske stap yn it produksjeproses fan healgeleiders, is direkt keppele oan chipprestaasjes, opbringst en produksjekosten.
#01 Eftergrûn en betsjutting fan wafersnijen
1.1 Definysje fan waferblokjes
Waferdicing (ek wol bekend as scribing) is in essensjele stap yn 'e produksje fan healgeleiders, rjochte op it ferdielen fan ferwurke wafers yn meardere yndividuele dies. Dizze dies befetsje typysk folsleine circuitfunksjonaliteit en binne de kearnkomponinten dy't úteinlik brûkt wurde yn 'e produksje fan elektroanyske apparaten. Om't chipûntwerpen komplekser wurde en de dimensjes bliuwe krimpen, wurde de presyzje- en effisjinsje-easken foar waferdicingtechnology hieltyd stranger.
Yn praktyske operaasjes brûkt wafer-snijwurk typysk ark mei hege presyzje lykas diamantmessen om te soargjen dat elke matrijs yntakt en folslein funksjoneel bliuwt. Wichtige stappen omfetsje tarieding foar it snijden, krekte kontrôle tidens it snijproses en kwaliteitsynspeksje nei it snijden.
Foar it snijen moat de wafer markearre en posysjonearre wurde om krekte snijpaden te garandearjen. Tidens it snijen moatte parameters lykas arkdruk en snelheid strang kontroleare wurde om skea oan 'e wafer te foarkommen. Nei it snijen wurde wiidweidige kwaliteitsynspeksjes útfierd om te soargjen dat elke chip foldocht oan prestaasjenormen.
De fûnemintele prinsipes fan wafer-dicingtechnology omfetsje net allinich de seleksje fan snijapparatuer en it ynstellen fan prosesparameters, mar ek de ynfloed fan 'e meganyske eigenskippen en skaaimerken fan materialen op' e snijkwaliteit. Bygelyks, leech-k diëlektryske silisiumwafers binne, fanwegen har mindere meganyske eigenskippen, tige gefoelich foar spanningskonsintraasje tidens it snijden, wat liedt ta storingen lykas chippen en barsten. De lege hurdens en brosheid fan leech-k materialen meitsje se gefoeliger foar strukturele skea ûnder meganyske krêft of termyske stress, benammen tidens it snijden. It kontakt tusken it ark en it waferoerflak, keppele oan hege temperatueren, kin de spanningskonsintraasje fierder fergrutsje.
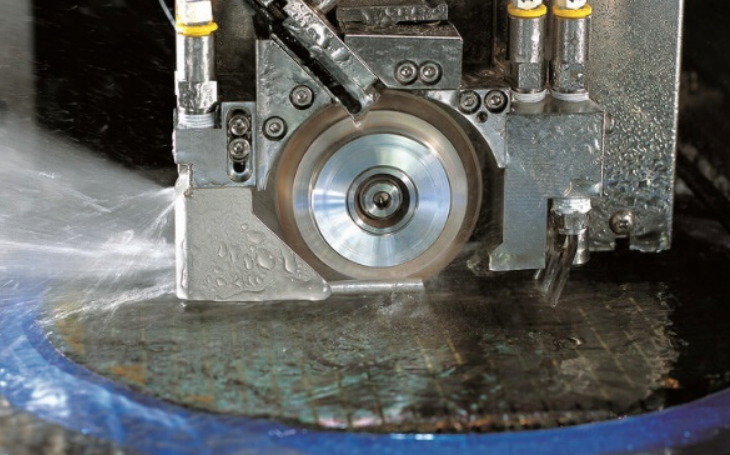
Mei foarútgong yn materiaalwittenskip is de technology foar it snijden fan wafers útwreide bûten tradisjonele healgeleiders op silisiumbasis om nije materialen lykas galliumnitride (GaN) op te nimmen. Dizze nije materialen, fanwegen har hurdens en strukturele eigenskippen, stelle nije útdagings foar snijprosessen, wêrtroch fierdere ferbetteringen yn snijgereedschap en techniken nedich binne.
As in kritysk proses yn 'e healgeleideryndustry wurdt wafer-dicing fierder optimalisearre yn reaksje op ûntwikkeljende easken en technologyske foarútgong, wêrtroch't de basis lein wurdt foar takomstige mikro-elektroanika en yntegreare circuittechnologyen.
Ferbetteringen yn wafer-dicingtechnology geane fierder as de ûntwikkeling fan helpmaterialen en ark. Se omfetsje ek prosesoptimalisaasje, ferbetteringen yn apparatuerprestaasjes en krekte kontrôle fan dicingparameters. Dizze foarútgong is bedoeld om hege presyzje, effisjinsje en stabiliteit yn it wafer-dicingproses te garandearjen, en te foldwaan oan 'e needsaak fan' e healgeleideryndustry foar lytsere dimensjes, hegere yntegraasje en kompleksere chipstrukturen.
ferbetteringsgebiet | Spesifike maatregels | Effekten |
Prosesoptimalisaasje | - Ferbetterje de earste tariedings, lykas krekter waferposysjonearring en paadplanning. | - Ferminderje snijflaters en ferbetterje stabiliteit. |
- Minimalisearje snijflaters en ferbetterje stabiliteit. | - Meitsje gebrûk fan real-time monitoring- en feedbackmeganismen om arkdruk, snelheid en temperatuer oan te passen. | |
- Ferlege waferbrekingssifers en ferbetterje chipkwaliteit. | ||
Ferbettering fan apparatuerprestaasjes | - Brûk hege-presyzje meganyske systemen en avansearre automatisearringskontrôletechnology. | - Ferbetterje de snijnauwkeurigens en ferminderje materiaalfergriemerij. |
- Yntrodusearje lasersnijtechnology dy't geskikt is foar wafers mei hege hurdens. | - Ferbetterje produksjeeffisjinsje en ferminderje hânmjittige flaters. | |
- Fergrutsje de automatisearring fan apparatuer foar automatyske monitoaring en oanpassingen. | ||
Presise parameterkontrôle | - Pas parameters lykas snijdjipte, snelheid, arktype en koelmetoaden fyn oan. | - Soargje foar de yntegriteit fan 'e die en elektryske prestaasjes. |
- Pas parameters oan op basis fan wafermateriaal, dikte en struktuer. | - Ferheegje opbringst, ferminderje materiaalôffal en ferleegje produksjekosten. | |
Strategyske betsjutting | - Kontinu nije technologyske paden ferkenne, prosessen optimalisearje en apparatuermooglikheden ferbetterje om te foldwaan oan merkfragen. | - Ferbetterje de opbringst en prestaasjes fan chipproduksje, en stypje de ûntwikkeling fan nije materialen en avansearre chipûntwerpen. |
1.2 It belang fan wafersnijen
Waferdicing spilet in krúsjale rol yn it produksjeproses fan healgeleiders, en hat in direkte ynfloed op de folgjende stappen, lykas de kwaliteit en prestaasjes fan it einprodukt. It belang dêrfan kin as folget detaillearre wurde:
Earst binne de krektens en konsistinsje fan it snijden fan stikken essensjeel foar it garandearjen fan chipopbringst en betrouberens. Tidens de produksje ûndergeane wafers meardere ferwurkingsstappen om ferskate yngewikkelde circuitstrukturen te foarmjen, dy't presys moatte wurde ferdield yn yndividuele chips (dies). As der wichtige flaters binne yn 'e ôfstimming of it snijden tidens it snijproses, kinne de circuits skansearre reitsje, wat de funksjonaliteit en betrouberens fan 'e chip beynfloedet. Dêrom soarget hege-presyzje-snijtechnology net allinich foar de yntegriteit fan elke chip, mar foarkomt ek skea oan ynterne circuits, wêrtroch't de totale opbringst ferbetteret.
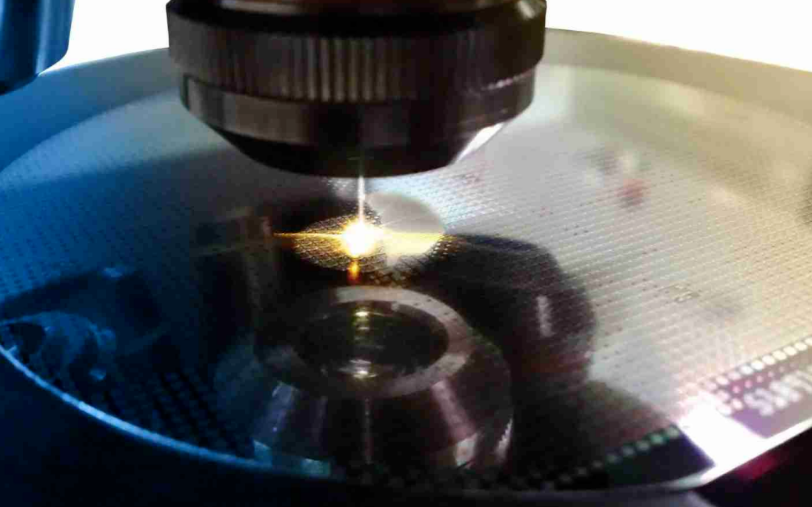
Twadder hat waferdicing in wichtige ynfloed op produksjeeffisjinsje en kostenkontrôle. As in krúsjale stap yn it produksjeproses beynfloedet de effisjinsje direkt de foarútgong fan folgjende stappen. Troch it dicingproses te optimalisearjen, automatisearringsnivo's te ferheegjen en snijsnelheden te ferbetterjen, kin de algemiene produksjeeffisjinsje sterk ferbettere wurde.
Oan 'e oare kant is materiaalfergriemerij by it snijden fan blokjes in krityske faktor yn kostenbehear. It brûken fan avansearre blokjestechnologyen ferminderet net allinich ûnnedige materiaalferlies tidens it snijproses, mar fergruttet ek it gebrûk fan wafers, wêrtroch't de produksjekosten ferlege wurde.
Mei foarútgong yn healgeleidertechnology bliuwe waferdiameters tanimme, en de circuitdichtheden nimme dêrtroch ta, wat hegere easken stelt oan 'e dicingtechnology. Gruttere wafers fereaskje krektere kontrôle fan snijpaden, foaral yn gebieten mei hege tichtheid fan circuits, dêr't sels lytse ôfwikingen meardere chips defekt meitsje kinne. Derneist omfetsje gruttere wafers mear snijlinen en kompleksere prosesstappen, wat fierdere ferbetteringen yn 'e presyzje, konsistinsje en effisjinsje fan dicingtechnologyen nedich makket om dizze útdagings oan te gean.
1.3 Waferblokjesproses
It proses fan it snijden fan wafers omfettet alle stappen fan 'e tariedingsfaze oant de definitive kwaliteitsynspeksje, wêrby't elke faze kritysk is foar it garandearjen fan 'e kwaliteit en prestaasjes fan 'e snijde chips. Hjirûnder is in detaillearre útlis fan elke faze.
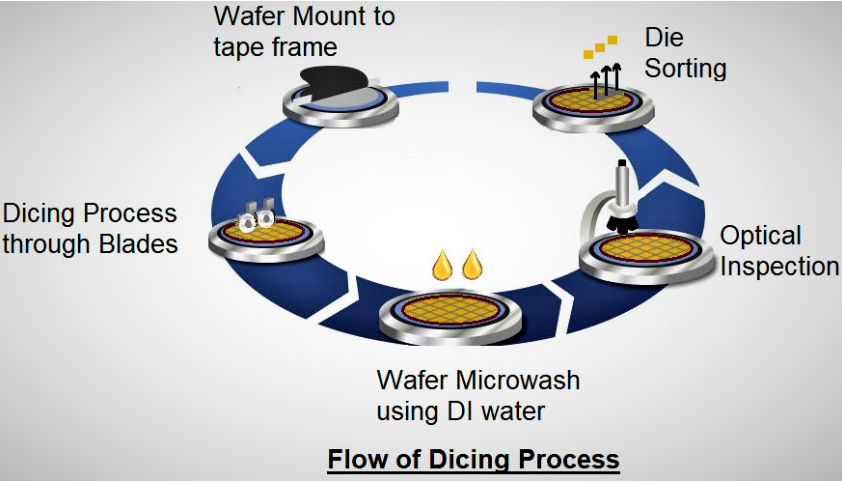
Faze | Detaillearre beskriuwing |
Tariedingsfaze | -WaferreinigingBrûk wetter mei hege suverens en spesjalisearre skjinmaakmiddels, kombinearre mei ultrasone of meganyske skrobjen, om ûnreinheden, dieltsjes en fersmoarging te ferwiderjen, wêrtroch in skjin oerflak garandearre wurdt. -Presise posysjonearringBrûk apparatuer mei hege presyzje om te soargjen dat de wafer sekuer ferdield wurdt lâns de ûntworpen snijpaden. -WaferfixaasjeBefestigje de wafer oan in tapeframe om stabiliteit te behâlden tidens it snijden, wêrtroch skea troch trilling of beweging foarkomt. |
Snijfase | -Blade SnijdenBrûk hege-snelheid rotearjende diamant-coated messen foar fysyk snijden, geskikt foar silisium-basearre materialen en kosten-effektyf. -Laser-snijwurkBrûk hege-enerzjy laserstrielen foar kontaktloos snijden, ideaal foar brosse of hurde materialen lykas galliumnitride, en biedt hegere presyzje en minder materiaalferlies. -Nije technologyenYntrodusearje laser- en plasmasnijtechnologyen om effisjinsje en presyzje fierder te ferbetterjen, wylst waarmte-beynfloede sônes minimalisearre wurde. |
Reinigingsfaze | - Brûk deionisearre wetter (DI-wetter) en spesjalisearre skjinmakmiddels, kombineare mei ultrasone of spuitreiniging, om pún en stof te ferwiderjen dat ûntstiet by it snijen, wêrtroch't foarkommen wurdt dat resten ynfloed hawwe op folgjende prosessen of de elektryske prestaasjes fan 'e chip. - Heechsuver DI-wetter foarkomt it yntrodusearjen fan nije fersmoargjende stoffen, wêrtroch in skjinne waferomjouwing garandearre wurdt. |
Ynspeksjefase | -Optyske ynspeksjeBrûk optyske deteksjesystemen yn kombinaasje mei AI-algoritmen om defekten fluch te identifisearjen, sadat der gjin barsten of chippen yn 'e sniene chips binne, de ynspeksje-effisjinsje ferbetteret en minsklike flaters ferminderje. -DiminsjemjittingFerifiearje dat de chipôfmjittings foldogge oan de ûntwerpspesifikaasjes. -Elektryske prestaasjetestsSoargje derfoar dat de elektryske prestaasjes fan krityske chips oan noarmen foldogge, wêrtroch betrouberens yn folgjende tapassingen garandearre wurdt. |
Sortearfaze | - Brûk robotearmen of fakuümsûgnappen om kwalifisearre chips fan it tapeframe te skieden en se automatysk te sortearjen op basis fan prestaasjes, wêrtroch produksjeeffisjinsje en fleksibiliteit wurde garandearre, wylst de presyzje ferbettere wurdt. |
It proses fan wafersnijen omfettet it skjinmeitsjen, posysjonearjen, snijden, skjinmeitsjen, ynspeksje en sortearjen fan wafers, wêrby't elke stap kritysk is. Mei foarútgong yn automatisearring, lasersnijden en AI-ynspeksjetechnologyen kinne moderne wafersnijsystemen hegere presyzje, snelheid en leger materiaalferlies berikke. Yn 'e takomst sille nije snijtechnologyen lykas laser en plasma stadichoan tradisjoneel blêdsnijden ferfange om te foldwaan oan 'e behoeften fan hieltyd kompleksere chipûntwerpen, wat de ûntwikkeling fan healgeleiderproduksjeprosessen fierder oandriuwt.
Wafer Cutting Technology en har prinsipes
De ôfbylding yllustrearret trije mienskiplike wafer-snijtechnologyen:Blade Snijden,Laser-snijwurk, enPlasma-snijwurkHjirûnder is in detaillearre analyze en oanfoljende útlis fan dizze trije techniken:
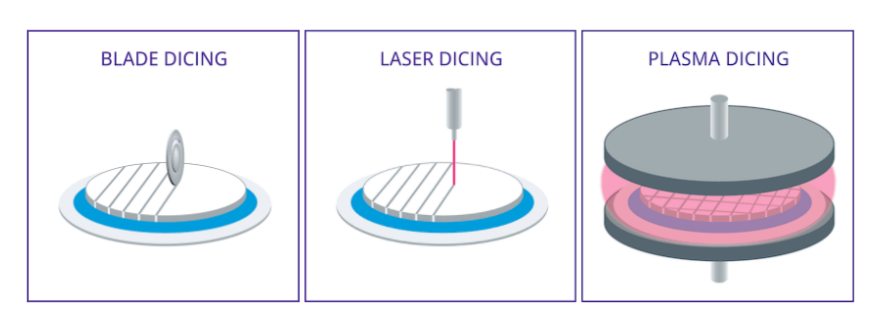
Yn 'e produksje fan healgeleiders is wafersnijden in krúsjale stap dy't it selektearjen fan 'e juste snijmetoade fereasket op basis fan 'e dikte fan' e wafer. De earste stap is it bepalen fan 'e dikte fan' e wafer. As de waferdikte mear as 100 mikron is, kin blêdsnijden keazen wurde as de snijmetoade. As blêdsnijden net geskikt is, kin de breuksnijmetoade brûkt wurde, dy't sawol krissnijden as blêdsnijdentechniken omfettet.
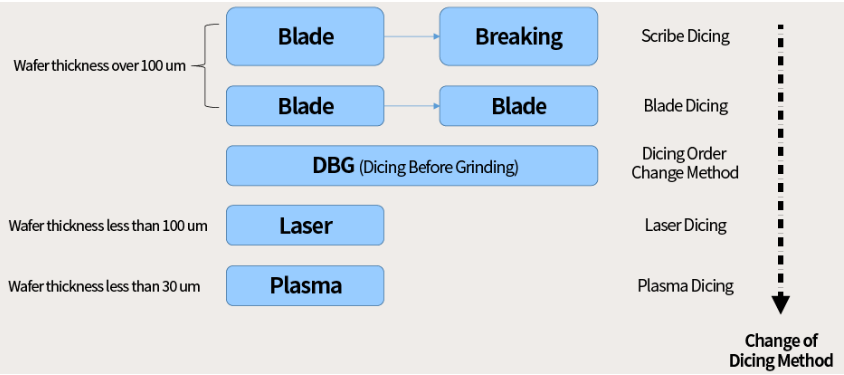
As de waferdikte tusken de 30 en 100 mikron leit, wurdt de DBG (Dice Before Grinding) metoade oanrikkemandearre. Yn dit gefal kin krissnijden, blêdsnijden, of it oanpassen fan de snijsekwinsje nei behoefte keazen wurde om de bêste resultaten te berikken.
Foar ultratinne wafers mei in dikte fan minder as 30 mikron wurdt lasersnijden de foarkarsmetoade fanwegen syn fermogen om tinne wafers presys te snijen sûnder oermjittige skea te feroarsaakjen. As lasersnijden net oan spesifike easken foldocht, kin plasmasnijden as alternatyf brûkt wurde. Dizze flowchart jout in dúdlik beslútfoarmingspad om te soargjen dat de meast geskikte wafersnijtechnology keazen wurdt ûnder ferskate diktebetingsten.
2.1 Mechanyske snijtechnology
Mechanyske snijtechnology is de tradisjonele metoade yn wafer-snijwurk. It kearnprinsipe is om in hege-snelheid rotearjende diamantslypskiif te brûken as snijark om de wafer te snijen. Wichtige apparatuer omfettet in loftlagerspindel, dy't it diamantslypskiifark mei hege snelheden oandriuwt om presys te snijen of te groeven lâns in foarôf definieare snijpaad. Dizze technology wurdt breed brûkt yn 'e yndustry fanwegen syn lege kosten, hege effisjinsje en brede tapassingsmooglikheden.
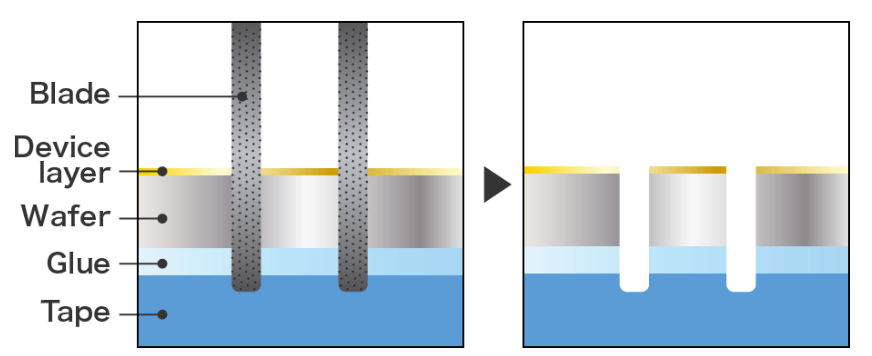
Foardielen
De hege hurdens en slijtvastheid fan diamantslypskiven meitsje it mooglik foar meganyske snijtechnology om oan te passen oan 'e snijbehoeften fan ferskate wafermaterialen, of it no giet om tradisjonele materialen op basis fan silisium of nijere gearstalde healgeleiders. De wurking is ienfâldich, mei relatyf lege technyske easken, wat de populariteit yn massaproduksje fierder befoarderet. Derneist, yn ferliking mei oare snijmetoaden lykas lasersnijden, hat meganysk snijden mear kontrolearbere kosten, wêrtroch it geskikt is foar produksjebehoeften yn grutte folumes.
Beperkingen
Nettsjinsteande syn talleaze foardielen hat meganyske snijtechnology ek beheiningen. Earst, troch it fysike kontakt tusken it ark en de wafer, is de snijpresyzje relatyf beheind, wat faak liedt ta dimensjonele ôfwikingen dy't de krektens fan lettere chipferpakking en testen kinne beynfloedzje. Twadder kinne defekten lykas chippen en barsten maklik foarkomme tidens it meganyske snijproses, wat net allinich de opbringst beynfloedet, mar ek de betrouberens en libbensdoer fan 'e chips negatyf kin beynfloedzje. De skea troch meganyske stress is benammen skealik foar chipproduksje mei hege tichtheid, foaral by it snijden fan brosse materialen, wêr't dizze problemen promininter binne.
Technologyske ferbetteringen
Om dizze beheiningen te oerwinnen, optimalisearje ûndersikers it meganyske snijproses kontinu. Wichtige ferbetterings omfetsje it ferbetterjen fan it ûntwerp en de materiaalseleksje fan slypskiven om de snijpresyzje en duorsumens te ferbetterjen. Derneist hat it optimalisearjen fan it strukturele ûntwerp en de kontrôlesystemen fan snijapparatuer de stabiliteit en automatisearring fan it snijproses fierder ferbettere. Dizze foarútgong ferminderje flaters feroarsake troch minsklike operaasjes en ferbetterje de konsistinsje fan 'e snijden. De ynfiering fan avansearre ynspeksje- en kwaliteitskontrôletechnologyen foar real-time monitoring fan anomalieën tidens it snijproses hat ek de betrouberens en opbringst fan it snijen signifikant ferbettere.
Takomstige ûntwikkeling en nije technologyen
Hoewol meganyske snijtechnology noch altyd in wichtige posysje ynnimt yn it snijden fan wafers, ûntwikkelje nije snijtechnologyen har rap as healgeleiderprosessen evoluearje. Bygelyks, de tapassing fan termyske lasersnijtechnology biedt nije oplossingen foar de presyzje- en defektproblemen by meganysk snijden. Dizze kontaktleaze snijmetoade ferminderet de fysike stress op 'e wafer, wêrtroch't it foarkommen fan chippen en barsten signifikant ferminderet, foaral by it snijden fan brossere materialen. Yn 'e takomst sil de yntegraasje fan meganyske snijtechnology mei opkommende snijtechniken healgeleiderproduksje mear opsjes en fleksibiliteit jaan, wêrtroch't de produksjeeffisjinsje en chipkwaliteit fierder ferbettere wurde.
Konklúzjend, hoewol meganyske snijtechnology bepaalde neidielen hat, meitsje trochgeande technologyske ferbetteringen en de yntegraasje dêrfan mei nije snijtechniken it mooglik om noch altyd in wichtige rol te spyljen yn 'e produksje fan healgeleiders en syn konkurrinsjefermogen yn takomstige prosessen te behâlden.
2.2 Lasersnijtechnology
Lasersnijtechnology, as in nije metoade yn it snijden fan wafers, hat stadichoan in soad omtinken krigen yn 'e healgeleideryndustry fanwegen syn hege presyzje, gebrek oan meganyske kontaktskea en rappe snijmooglikheden. Dizze technology brûkt de hege enerzjytichtens en fokussearringsfermogen fan in laserstraal om in lytse waarmte-beynfloede sône op it oerflak fan it wafermateriaal te meitsjen. As de laserstraal op 'e wafer tapast wurdt, feroarsaket de generearre termyske spanning dat it materiaal brekt op 'e oanwiisde lokaasje, wêrtroch presys snijden berikt wurdt.
Foardielen fan lasersnijtechnology
• Hege presyzjeDe krekte posysjonearringsmooglikheden fan 'e laserstraal meitsje snijpresyzje op mikron- of sels nanometernivo mooglik, en foldocht oan 'e easken fan moderne hege-presyzje, hege-tichtens yntegreare sirkwyproduksje.
• Gjin meganysk kontaktLasersnijden foarkomt fysyk kontakt mei de wafer, wêrtroch't mienskiplike problemen by meganysk snijden, lykas chippen en barsten, foarkomt, wêrtroch't de opbringst en betrouberens fan 'e chips signifikant ferbettere wurde.
• Snelle snijsnelheidDe hege snelheid fan lasersnijden draacht by oan ferhege produksjeeffisjinsje, wêrtroch it foaral geskikt is foar grutskalige produksjescenario's mei hege snelheid.
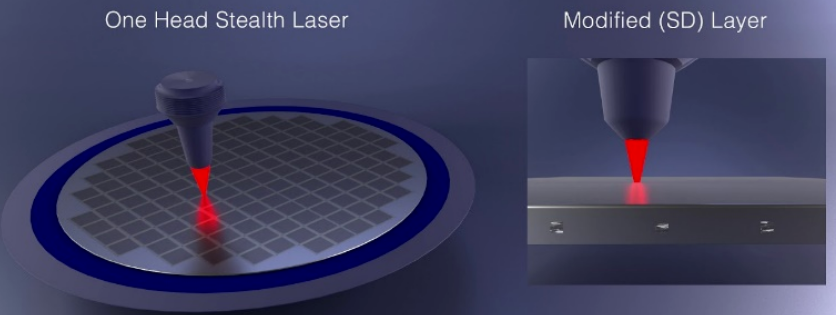
Útdagings dy't tsjinkamen
• Hege apparatuerkostenDe earste ynvestearring foar lasersnijapparatuer is heech, wat ekonomyske druk foarmet, foaral foar lytse oant middelgrutte produksjebedriuwen.
• Komplekse proseskontrôleLasersnijden fereasket krekte kontrôle fan ferskate parameters, ynklusyf enerzjytichtens, fokusposysje en snijsnelheid, wêrtroch it proses kompleks is.
• Problemen mei troch waarmte beynfloede sônesHoewol't it kontaktleaze karakter fan lasersnijden meganyske skea ferminderet, kin de termyske stress feroarsake troch de waarmte-beynfloede sône (HAZ) in negative ynfloed hawwe op 'e eigenskippen fan it wafermateriaal. Fierdere optimalisaasje fan it proses is nedich om dit effekt te minimalisearjen.
Rjochtingen foar technologyske ferbettering
Om dizze útdagings oan te pakken, rjochtsje ûndersikers har op it ferleegjen fan apparatuerkosten, it ferbetterjen fan snijeffisjinsje en it optimalisearjen fan 'e prosesstream.
• Effisjinte lasers en optyske systemenTroch it ûntwikkeljen fan effisjintere lasers en avansearre optyske systemen is it mooglik om apparatuerkosten te ferleegjen, wylst de snijpresyzje en snelheid ferbettere wurde.
• Optimalisearjen fan prosesparametersDer wurdt yngeand ûndersyk dien nei de ynteraksje tusken lasers en wafermaterialen om prosessen te ferbetterjen dy't de waarmte-beynfloede sône ferminderje, wêrtroch't de snijkwaliteit ferbetteret.
• Intelligente kontrôlesystemenDe ûntwikkeling fan yntelliginte kontrôletechnologyen hat as doel it lasersnijproses te automatisearjen en te optimalisearjen, wêrtroch de stabiliteit en konsistinsje ferbettere wurde.
Lasersnijtechnology is benammen effektyf yn ultratinne wafers en hege-presyzje snijscenario's. As wafergruttes tanimme en circuitdichtheden tanimme, hawwe tradisjonele meganyske snijmetoaden muoite om te foldwaan oan 'e hege-presyzje en hege-effisjinsje easken fan moderne healgeleiderproduksje. Fanwegen syn unike foardielen wurdt lasersnijden de foarkarsoplossing yn dizze fjilden.
Hoewol lasersnijtechnology noch altyd te krijen hat mei útdagings lykas hege apparatuerkosten en proseskompleksiteit, meitsje de unike foardielen yn hege presyzje en kontaktleaze skea it in wichtige rjochting foar ûntwikkeling yn 'e produksje fan healgeleiders. Mei de trochgeande foarútgong fan lasertechnology en yntelliginte kontrôlesystemen wurdt ferwachte dat lasersnijden de effisjinsje en kwaliteit fan wafersnijden fierder sil ferbetterje, wat de trochgeande ûntwikkeling fan 'e healgeleideryndustry sil oandriuwe.
2.3 Plasma-snijtechnology
Plasma-snijtechnology, as in opkommende wafer-snijmetoade, hat de lêste jierren flinke oandacht krigen. Dizze technology brûkt hege-enerzjy plasmastrielen om wafers presys te snijen troch de enerzjy, snelheid en snijpaad fan 'e plasmastriel te kontrolearjen, wêrtroch optimale snijresultaten berikt wurde.
Wurkprinsipe en foardielen
It proses fan plasmasnijden is basearre op in plasmastriel mei hege temperatuer en hege enerzjy dy't troch de apparatuer generearre wurdt. Dizze striel kin it wafermateriaal yn in heul koarte tiid ferwaarmje oant it smelt- of ferdampingspunt, wêrtroch't fluch snijden mooglik is. Yn ferliking mei tradisjoneel meganysk of lasersnijden is plasmasnijden rapper en produseart it in lytsere waarmte-beynfloede sône, wêrtroch't it foarkommen fan skuorren en skea tidens it snijden effektyf ferminderet.
Yn praktyske tapassingen is plasmasnijtechnology benammen goed yn it omgean mei wafers mei komplekse foarmen. De hege-enerzjy, ferstelbere plasmastriel kin maklik unregelmjittich foarme wafers mei hege presyzje snije. Dêrom is dizze technology yn 'e mikro-elektroanikaproduksje, benammen yn oanpaste en lytse-batchproduksje fan high-end chips, tige beloftefol foar wiidferspraat gebrûk.
Útdagings en beheiningen
Nettsjinsteande de protte foardielen fan plasmasnijtechnology, stiet it ek foar wat útdagings.
• Kompleks prosesIt plasmasnijproses is kompleks en fereasket apparatuer mei hege presyzje en betûfte operators om te garandearjenkrektens en stabiliteit by it snijden.
• Miljeukontrôle en feiligensDe hege temperatuer, hege-enerzjy aard fan 'e plasmastriel fereasket strange miljeukontrôle en feiligensmaatregels, wat de kompleksiteit en kosten fan ymplemintaasje fergruttet.
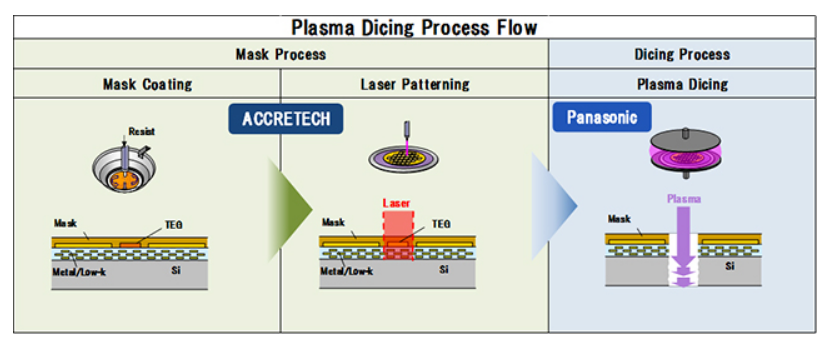
Takomstige ûntwikkelingsrjochtingen
Mei technologyske foarútgong wurdt ferwachte dat de útdagings dy't ferbûn binne mei plasmasnijden stadichoan oerwûn wurde. Troch it ûntwikkeljen fan tûkere en stabiler snijapparatuer kin de ôfhinklikens fan hânmjittige operaasjes wurde fermindere, wêrtroch de produksjeeffisjinsje ferbettere wurdt. Tagelyk sil it optimalisearjen fan prosesparameters en de snijomjouwing helpe om feiligensrisiko's en operasjonele kosten te ferminderjen.
Yn 'e healgeleideryndustry binne ynnovaasjes yn wafer-snij- en blokjesnijtechnology krúsjaal foar it befoarderjen fan 'e ûntwikkeling fan' e yndustry. Plasma-snijtechnology, mei syn hege presyzje, effisjinsje en fermogen om komplekse waferfoarmen te behanneljen, is ûntstien as in wichtige nije spiler yn dit fjild. Hoewol't der noch guon útdagings binne, sille dizze problemen stadichoan oanpakt wurde mei trochgeande technologyske ynnovaasje, wêrtroch't mear mooglikheden en kânsen foar de produksje fan healgeleiders brocht wurde.
De tapassingsperspektiven fan plasmasnijtechnology binne enoarm, en it wurdt ferwachte dat it yn 'e takomst in wichtiger rol sil spylje yn 'e produksje fan healgeleiders. Troch trochgeande technologyske ynnovaasje en optimalisaasje sil plasmasnijden net allinich besteande útdagings oanpakke, mar ek in krêftige driuwfear wurde foar de groei fan 'e healgeleideryndustry.
2.4 Snijkwaliteit en ynfloedrike faktoaren
De kwaliteit fan it snijden fan wafers is krúsjaal foar de neifolgjende chipferpakking, testen, en de algemiene prestaasjes en betrouberens fan it einprodukt. Faak foarkommende problemen dy't foarkomme by it snijden binne barsten, chippen en snijôfwikingen. Dizze problemen wurde beynfloede troch ferskate faktoaren dy't tegearre wurkje.
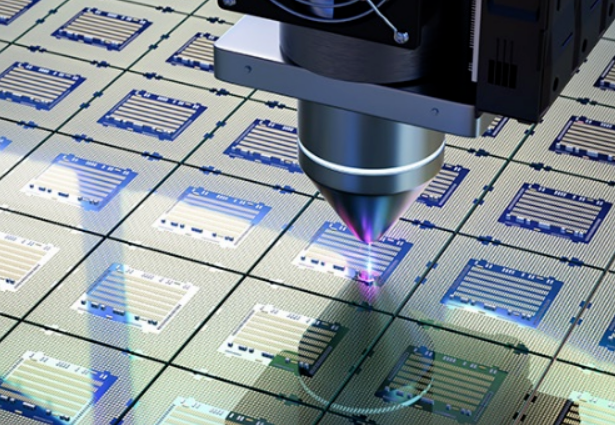
Kategory | Ynhâld | Ynfloed |
Prosesparameters | Snijsnelheid, feedsnelheid en snijdjipte hawwe direkt ynfloed op de stabiliteit en presyzje fan it snijproses. Ferkearde ynstellingen kinne liede ta spanningskonsintraasje en in te hege waarmte-beynfloede sône, wat resulteart yn skuorren en ôfbrokkeljen. It passend oanpassen fan parameters op basis fan wafermateriaal, dikte en snijeasken is de kaai foar it berikken fan de winske snijresultaten. | De juste prosesparameters soargje foar presys snijden en ferminderje it risiko op defekten lykas skuorren en ôfbrokkeljen. |
Apparatuer- en materiaalfaktoaren | -Kwaliteit fan it blêdIt materiaal, de hurdens en de slijtvastheid fan it blêd beynfloedzje de glêdens fan it snijproses en de flakheid fan it snijflak. Minne kwaliteitsblêden ferheegje wriuwing en termyske stress, wat mooglik kin liede ta skuorren of ôfbrokkeljen. It kiezen fan it juste blêdmateriaal is krúsjaal. -KoelmiddelprestaasjesKoelmiddels helpe by it ferminderjen fan snijtemperatuer, it minimalisearjen fan wriuwing en it fuortheljen fan pún. Ineffektive koelmiddels kinne liede ta hege temperatueren en púnopbou, wat ynfloed hat op 'e snijkwaliteit en effisjinsje. It selektearjen fan effisjinte en miljeufreonlike koelmiddels is essensjeel. | De kwaliteit fan it blêd beynfloedet de presyzje en glêdens fan 'e snede. Ineffektive koelmiddel kin liede ta minne snijkwaliteit en effisjinsje, wat de needsaak foar optimaal gebrûk fan koelmiddel beklammet. |
Proseskontrôle en kwaliteitsynspeksje | -ProseskontrôleReal-time monitoring en oanpassing fan wichtige snijparameters om stabiliteit en konsistinsje yn it snijproses te garandearjen. -KwaliteitsynspeksjeKontrôles fan it uterlik nei it snijen, dimensjonele mjittingen en elektryske prestaasjestests helpe by it fluch identifisearjen en oanpakken fan kwaliteitsproblemen, wêrtroch't de snijkrektens en konsistinsje ferbettere wurde. | Juiste proseskontrôle en kwaliteitsynspeksje helpe om konsekwinte, heechweardige snijresultaten en iere deteksje fan potinsjele problemen te garandearjen. |

Ferbetterjen fan snijkwaliteit
It ferbetterjen fan de snijkwaliteit fereasket in wiidweidige oanpak dy't rekken hâldt mei prosesparameters, apparatuer- en materiaalseleksje, proseskontrôle en ynspeksje. Troch snijtechnologyen kontinu te ferbetterjen en prosesmetoaden te optimalisearjen, kin de presyzje en stabiliteit fan wafersnijden fierder ferbettere wurde, wêrtroch't betrouberdere technyske stipe foar de healgeleiderproduksje-yndustry levere wurdt.
#03 Hantering en testen nei it snijen
3.1 Reiniging en Droeging
De skjinmeits- en droechstappen nei it snijden fan wafers binne krúsjaal foar it garandearjen fan de kwaliteit fan 'e chip en de soepele foarútgong fan folgjende prosessen. Tidens dizze faze is it essensjeel om silikonresten, koelmiddelresten en oare fersmoargingen dy't by it snijden ûntstien binne, yngeand te ferwiderjen. It is like wichtich om te soargjen dat de chips net skansearre wurde tidens it skjinmeitsproses, en nei it droegjen, te soargjen dat der gjin focht op it chipoerflak achterbliuwt om problemen lykas korrosje of elektrostatyske ûntlading te foarkommen.
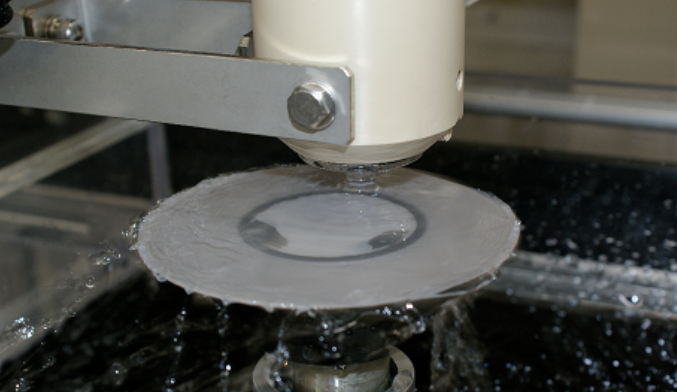
Behanneling nei it snijen: Reinigings- en droechproses
Prosesstap | Ynhâld | Ynfloed |
Reinigingsproses | -MetoadeBrûk spesjalisearre skjinmaakmiddels en suver wetter, kombinearre mei ultrasone of meganyske boarsteltechniken foar it skjinmeitsjen. | Soarget foar yngeande ferwidering fan fersmoarging en foarkomt skea oan 'e chips by it skjinmeitsjen. |
-Seleksje fan skjinmakmiddelsKies op basis fan wafermateriaal en type fersmoarging om effektive skjinmeitsjen te garandearjen sûnder de chip te beskeadigjen. | De juste seleksje fan middels is de kaai foar effektive skjinmeitsjen en beskerming tsjin splinters. | |
-ParameterkontrôleKontrolearje de skjinmaaktemperatuer, tiid en konsintraasje fan 'e skjinmaakoplossing strang om kwaliteitsproblemen te foarkommen dy't feroarsake wurde troch ferkearde skjinmeitsjen. | Kontrôles helpe om te foarkommen dat de wafer beskeadige wurdt of dat fersmoarging efterbliuwt, wêrtroch't in konsekwinte kwaliteit garandearre wurdt. | |
Droechproses | -Tradisjonele metoadenNatuerlike loftdroeging en waarme loftdroeging, dy't in lege effisjinsje hawwe en kinne liede ta opbou fan statyske elektrisiteit. | Kin liede ta stadiger droechtiden en potinsjele problemen mei statyske elektrisiteit. |
-Moderne technologyenBrûk avansearre technologyen lykas fakuümdroeging en ynfrareaddroeging om te soargjen dat chips fluch droegje en skealike effekten foarkomme. | Flugger en effisjinter droechproses, wêrtroch it risiko op statyske ûntlading of fochtrelatearre problemen ferminderet. | |
Seleksje en ûnderhâld fan apparatuer | -Seleksje fan apparatuerHeechprestaasjes skjinmaak- en droechmasines ferbetterje de ferwurkingseffisjinsje en kontrolearje potinsjele problemen by de ôfhanneling fyn. | Masines fan hege kwaliteit soargje foar bettere ferwurking en ferminderje de kâns op flaters by it skjinmeitsjen en droegjen. |
-Underhâld fan apparatuerRegelmjittige ynspeksje en ûnderhâld fan apparatuer soargje derfoar dat it yn optimale wurkjende steat bliuwt, wêrtroch't de chipkwaliteit garandearre wurdt. | Goed ûnderhâld foarkomt apparatuerfalen, wêrtroch betroubere en heechweardige ferwurking garandearre wurdt. |
Reiniging en droegjen nei it snijen
De skjinmeits- en droechstappen nei it snijden fan wafers binne komplekse en delikate prosessen dy't soarchfâldige ôfwaging fan meardere faktoaren fereaskje om it definitive ferwurkingsresultaat te garandearjen. Troch gebrûk te meitsjen fan wittenskiplike metoaden en strange prosedueres is it mooglik om te garandearjen dat elke chip de folgjende ferpakkings- en teststadia yn optimale steat yngiet.
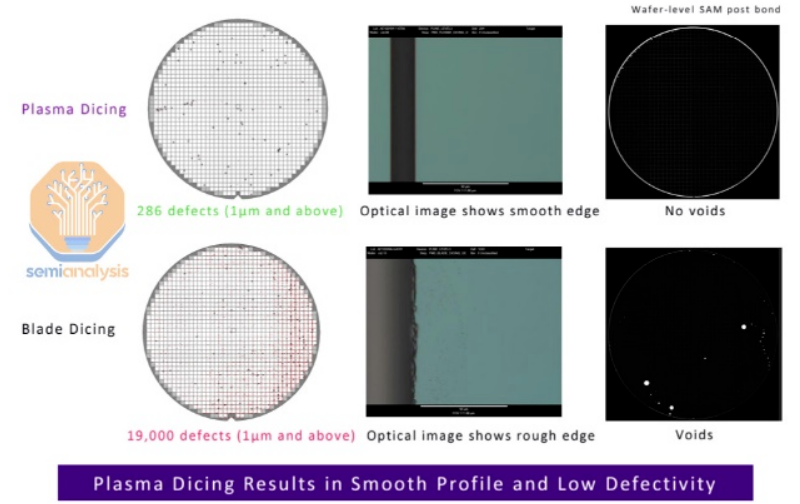
Ynspeksje en testen nei it snijen
Stap | Ynhâld | Ynfloed |
Ynspeksjestap | 1.Fisuele ynspeksjeBrûk fisuele of automatisearre ynspeksjeapparatuer om te kontrolearjen op sichtbere defekten lykas barsten, chippen of fersmoarging op it chipoerflak. Identifisearje fluch fysyk beskeadige chips om fergriemerij te foarkommen. | Helpt by it identifisearjen en eliminearjen fan defekte chips betiid yn it proses, wêrtroch materiaalferlies wurdt fermindere. |
2.Grutte mjittingBrûk presyzjemjitapparaten om de ôfmjittings fan 'e chip sekuer te mjitten, sadat de snijgrutte foldocht oan ûntwerpspesifikaasjes en prestaasjesproblemen of ferpakkingsproblemen foarkomme. | Soarget derfoar dat chips binnen de fereaske gruttegrinzen binne, wêrtroch prestaasjesfermindering of gearstallingsproblemen foarkomme. | |
3.Elektryske prestaasjetestsEvaluearje wichtige elektryske parameters lykas wjerstân, kapasitans en induktans, om net-konforme chips te identifisearjen en te soargjen dat allinich prestaasjekwalifisearre chips trochgean nei de folgjende faze. | Soarget derfoar dat allinich funksjonele en prestaasjetestte chips foarútgeane yn it proses, wêrtroch it risiko op falen yn lettere stadia ferminderet. | |
Teststap | 1.Funksjonele testenFerifiearje dat de basisfunksjonaliteit fan 'e chip wurket sa't bedoeld, en identifisearje en eliminearje chips mei funksjonele abnormaliteiten. | Soarget derfoar dat chips foldogge oan basis operasjonele easken foardat se trochgean nei lettere stadia. |
2.Betrouberens testenEvaluearje de stabiliteit fan chipprestaasjes ûnder lang gebrûk of rûge omjouwings, typysk mei ferâldering by hege temperatuer, testen by lege temperatuer en testen fan fochtigens om ekstreme omstannichheden yn 'e echte wrâld te simulearjen. | Soarget derfoar dat chips betrouber funksjonearje kinne ûnder in ferskaat oan miljeu-omstannichheden, wêrtroch't de libbensdoer en stabiliteit fan it produkt ferbettere wurde. | |
3.KompatibiliteitstestsFerifiearje dat de chip goed wurket mei oare komponinten of systemen, en soargje derfoar dat der gjin flaters of prestaasjefermindering binne fanwegen ynkompatibiliteit. | Soarget foar soepele wurking yn echte applikaasjes troch kompatibiliteitsproblemen te foarkommen. |
3.3 Ferpakking en opslach
Nei it snijden fan wafers binne de chips in krúsjale útfier fan it produksjeproses fan healgeleiders, en har ferpakkings- en opslachstadia binne like wichtich. Juiste ferpakkings- en opslachmaatregels binne essensjeel, net allinich om de feiligens en stabiliteit fan 'e chips te garandearjen tidens transport en opslach, mar ek foar it jaan fan sterke stipe foar folgjende produksje-, test- en ferpakkingsstadia.
Gearfetting fan ynspeksje- en teststadia:
De ynspeksje- en teststappen foar chips nei it snijden fan wafers dekke in ferskaat oan aspekten, ynklusyf fisuele ynspeksje, gruttemjitting, elektryske prestaasjetests, funksjonele testen, betrouberenstests en kompatibiliteitstests. Dizze stappen binne mei-inoar ferbûn en komplementêr, en foarmje in solide barriêre om produktkwaliteit en betrouberens te garandearjen. Troch strange ynspeksje- en testprosedueres kinne potinsjele problemen fluch identifisearre en oplost wurde, wêrtroch't derfoar soarge wurdt dat it einprodukt foldocht oan de easken en ferwachtingen fan 'e klant.
Aspekt | Ynhâld |
Ferpakkingsmaatregels | 1.AntistatyskFerpakkingsmaterialen moatte poerbêste antistatyske eigenskippen hawwe om te foarkommen dat statyske elektrisiteit de apparaten beskeadiget of har prestaasjes beynfloedet. |
2.FochtbestindichFerpakkingsmaterialen moatte in goede fochtbestindigens hawwe om korrosje en ferswakking fan elektryske prestaasjes feroarsake troch fochtigens te foarkommen. | |
3.SkokbestindichFerpakkingsmaterialen moatte effektive skokabsorpsje biede om de chips te beskermjen tsjin trillingen en ynfloeden tidens ferfier. | |
Opslachomjouwing | 1.FochtigenskontrôleKontrolearje de fochtigens strang binnen in passend berik om fochtopname en korrosje te foarkommen feroarsake troch tefolle fochtigens of statyske problemen feroarsake troch lege fochtigens. |
2.SkjinensHâld in skjinne opslachomjouwing yn stân om fersmoarging fan chips troch stof en ûnreinheden te foarkommen. | |
3.TemperatuerkontrôleStel in ridlik temperatuerberik yn en behâld temperatuerstabiliteit om fersnelde ferâldering te foarkommen troch tefolle waarmte of kondensaasjeproblemen feroarsake troch lege temperatueren. | |
Regelmjittige ynspeksje | Ynspektearje en evaluearje opsleine chips geregeld, mei help fan fisuele ynspeksjes, gruttemjittingen en elektryske prestaasjetests om potinsjele problemen op 'e tiid te identifisearjen en oan te pakken. Plan it gebrûk fan chips op basis fan opslachtiid en -omstannichheden om te soargjen dat se yn optimale steat brûkt wurde. |
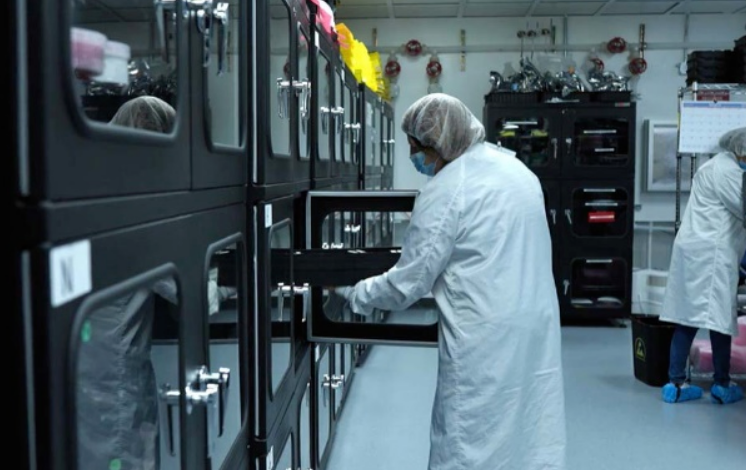
It probleem fan mikroskeuren en skea tidens it wafer-snijproses is in wichtige útdaging yn 'e produksje fan healgeleiders. De snijspanning is de primêre oarsaak fan dit ferskynsel, om't it lytse skuorren en skea op it waferoerflak feroarsaket, wat liedt ta ferhege produksjekosten en in fermindering fan produktkwaliteit.
Om dizze útdaging oan te pakken, is it krúsjaal om snijspanning te minimalisearjen en optimalisearre snijtechniken, ark en omstannichheden te ymplementearjen. Soarchfâldige oandacht foar faktoaren lykas blêdmateriaal, snijsnelheid, druk en koelmetoaden kin helpe om de foarming fan mikroskeuren te ferminderjen en de totale opbringst fan it proses te ferbetterjen. Derneist ûndersiket oanhâldend ûndersyk nei mear avansearre snijtechnologyen, lykas laserdicing, manieren om dizze problemen fierder te ferminderjen.
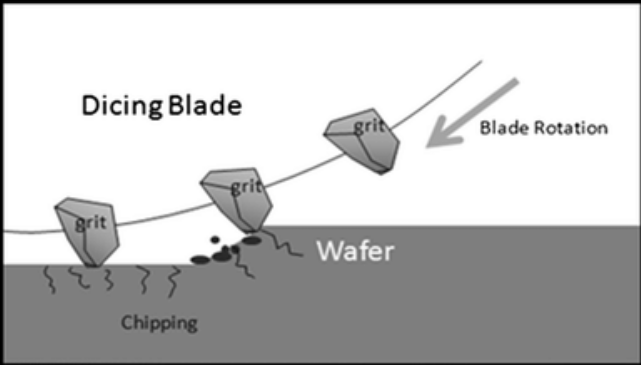
As in kwetsber materiaal binne wafers gefoelich foar ynterne strukturele feroarings as se ûnderwurpen wurde oan meganyske, termyske of gemyske stress, wat liedt ta de foarming fan mikroskeuren. Hoewol dizze skuorren miskien net direkt merkber binne, kinne se útwreidzje en slimmer skea feroarsaakje as it produksjeproses foarútgiet. Dit probleem wurdt foaral problematysk tidens folgjende ferpakkings- en teststadia, wêr't temperatuerfluktuaasjes en ekstra meganyske stress kinne feroarsaakje dat dizze mikroskeuren evoluearje ta sichtbere brekken, wat potinsjeel kin liede ta chipfalen.
Om dit risiko te ferminderjen, is it essensjeel om it snijproses sekuer te kontrolearjen troch parameters lykas snijsnelheid, druk en temperatuer te optimalisearjen. It brûken fan minder agressive snijmetoaden, lykas lasersnijden, kin de meganyske stress op 'e wafer ferminderje en de foarming fan mikroskeuren minimalisearje. Derneist kin it ymplementearjen fan avansearre ynspeksjemetoaden lykas ynfrareadscannen of röntgenôfbylding tidens it wafersnijproses helpe om dizze skuorren yn in ier stadium te detektearjen foardat se fierdere skea feroarsaakje.
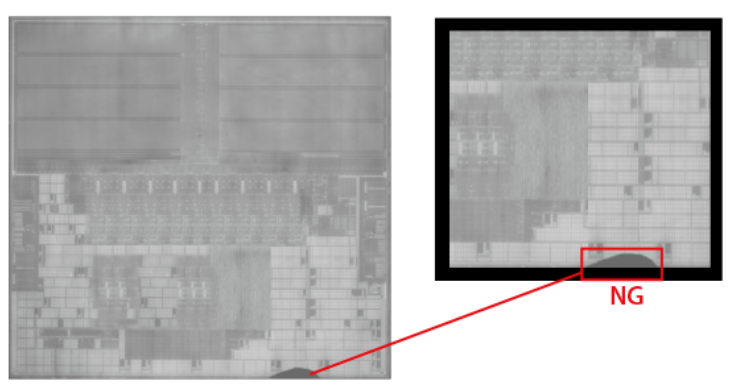
De skea oan it waferoerflak is in wichtige soarch yn it snijproses, om't it in direkte ynfloed hawwe kin op 'e prestaasjes en betrouberens fan' e chip. Sokke skea kin feroarsake wurde troch ferkeard gebrûk fan snijgereedschap, ferkearde snijparameters, of materiaaldefekten dy't ynherent binne oan 'e wafer sels. Wat de oarsaak ek is, dizze skea kin liede ta feroaringen yn 'e elektryske wjerstân of kapasitânsje fan it sirkwy, wat ynfloed hat op 'e algemiene prestaasjes.
Om dizze problemen oan te pakken, wurde twa wichtige strategyen ûndersocht:
1. Optimalisearjen fan snijgereedschap en parametersTroch skerpere messen te brûken, de snijsnelheid oan te passen en de snijdjipte te feroarjen, kin de spanningskonsintraasje tidens it snijproses minimalisearre wurde, wêrtroch de mooglikheid fan skea ferminderet.
2. Nije snijtechnologyen ferkenneAvansearre techniken lykas lasersnijden en plasmasnijden biede ferbettere presyzje, wylst se potinsjeel it nivo fan skea oan 'e wafer ferminderje. Dizze technologyen wurde bestudearre om manieren te finen om hege snijkrektens te berikken, wylst termyske en meganyske stress op 'e wafer minimalisearre wurdt.
Termysk ynfloedgebiet en syn effekten op prestaasjes
By termyske snijprosessen lykas laser- en plasmasnijden meitsje hege temperatueren ûnûntkomber in termyske ynfloedsône op it oerflak fan 'e wafer. Dit gebiet, dêr't de temperatuergradiïnt signifikant is, kin de eigenskippen fan it materiaal feroarje, wat ynfloed hat op 'e definitive prestaasjes fan 'e chip.
Ynfloed fan 'e termysk beynfloede sône (TAZ):
Feroarings yn kristalstruktuerUnder hege temperatueren kinne atomen yn it wafermateriaal opnij rangearje, wêrtroch't ferfoarmingen yn 'e kristalstruktuer ûntsteane. Dizze ferfoarming ferswakket it materiaal, wêrtroch't de meganyske sterkte en stabiliteit ferminderet, wat it risiko op chipfalen by gebrûk fergruttet.
Feroarings yn elektryske eigenskippenHege temperatueren kinne de konsintraasje en mobiliteit fan 'e drager yn healgeleidermaterialen feroarje, wat ynfloed hat op 'e elektryske gelieding en stroomoerdrachtseffisjinsje fan 'e chip. Dizze feroarings kinne liede ta in ôfname fan 'e chipprestaasjes, wêrtroch't de chip mooglik net geskikt is foar it bedoelde doel.
Om dizze effekten te ferminderjen, binne it kontrolearjen fan 'e temperatuer tidens it snijden, it optimalisearjen fan 'e snijparameters, en it ferkennen fan metoaden lykas koeljets of neiferwurkingsbehannelingen essensjele strategyen om de omfang fan 'e termyske ynfloed te ferminderjen en de yntegriteit fan it materiaal te behâlden.
Oer it algemien binne sawol mikroskeuren as termyske ynfloedsônes krúsjale útdagings yn waferdicingtechnology. Trochgeande ûndersyk, neist technologyske foarútgong en kwaliteitskontrôlemaatregels, sil nedich wêze om de kwaliteit fan healgeleiderprodukten te ferbetterjen en har merkkonkurrinsjefermogen te fergrutsjen.
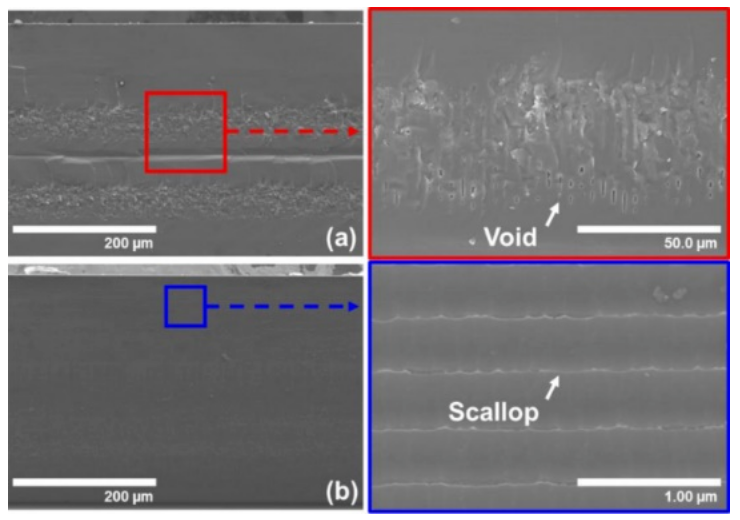
Maatregels om de termyske ynfloedsône te kontrolearjen:
Optimalisearjen fan snijprosesparametersIt ferminderjen fan de snijsnelheid en it fermogen kin de grutte fan 'e termyske ynfloedsône (TAZ) effektyf minimalisearje. Dit helpt by it kontrolearjen fan 'e hoemannichte waarmte dy't ûntstiet tidens it snijproses, wat direkt ynfloed hat op 'e materiaaleigenskippen fan 'e wafer.
Avansearre koeltechnologyenDe tapassing fan technologyen lykas koeling mei floeibere stikstof en mikrofluidyske koeling kin it berik fan 'e termyske ynfloedsône signifikant beheine. Dizze koelmetoaden helpe om waarmte effisjinter te fersprieden, wêrtroch't de materiaaleigenskippen fan 'e wafer bewarre wurde en termyske skea minimalisearre wurdt.
MateriaalseleksjeUndersykers ûndersykje nije materialen, lykas koalstofnanobuizen en grafeen, dy't in poerbêste termyske geliedingsfermogen en meganyske sterkte hawwe. Dizze materialen kinne de termyske ynfloedsône ferminderje, wylst se de algemiene prestaasjes fan 'e chips ferbetterje.
Gearfetsjend, hoewol de termyske ynfloedsône in ûnûntkomber gefolch is fan termyske snijtechnologyen, kin it effektyf kontroleare wurde troch optimalisearre ferwurkingstechniken en materiaalseleksje. Takomstich ûndersyk sil wierskynlik rjochte wêze op it fynôfstimmen en automatisearjen fan termyske snijprosessen om effisjintere en presysere waferdikking te berikken.

Balansstrategy:
It berikken fan de optimale lykwicht tusken waferopbringst en produksjeeffisjinsje is in oanhâldende útdaging yn waferdikkingtechnology. Fabrikanten moatte meardere faktoaren beskôgje, lykas merkfraach, produksjekosten en produktkwaliteit, om in rasjonele produksjestrategy en prosesparameters te ûntwikkeljen. Tagelyk binne it ynfieren fan avansearre snijapparatuer, it ferbetterjen fan operatorfeardigens en it ferbetterjen fan de kwaliteitskontrôle fan grûnstoffen essensjeel om de opbringst te behâlden of sels te ferbetterjen, wylst de produksjeeffisjinsje ferhege wurdt.
Takomstige útdagings en kânsen:
Mei de foarútgong fan healgeleidertechnology stiet wafersnijden foar nije útdagings en kânsen. As chipgruttes lytser wurde en yntegraasje tanimt, groeie de easken oan snijpresyzje en kwaliteit signifikant. Tagelyk leverje opkommende technologyen nije ideeën foar de ûntwikkeling fan wafersnijtechniken. Fabrikanten moatte ôfstimd bliuwe op merkdynamika en technologyske trends, en produksjestrategyen en prosesparameters kontinu oanpasse en optimalisearje om te foldwaan oan merkferoaringen en technologyske easken.
Konklúzjend, troch it yntegrearjen fan oerwagings fan merkfraach, produksjekosten en produktkwaliteit, en troch it yntrodusearjen fan avansearre apparatuer en technology, it ferbetterjen fan operatorfeardigens, en it fersterkjen fan grûnstofkontrôle, kinne fabrikanten de bêste lykwicht berikke tusken waferopbringst en produksjeeffisjinsje tidens waferdicing, wat liedt ta effisjinte en heechweardige produksje fan healgeleiderprodukten.
Takomstige útsjoch:
Mei rappe technologyske foarútgong nimt de healgeleidertechnology yn in noch nea earder sjoen tempo ta. As in krityske stap yn 'e produksje fan healgeleiders is wafer-snijtechnology ree foar spannende nije ûntwikkelingen. Mei it each op de takomst wurdt ferwachte dat wafer-snijtechnology wichtige ferbetteringen sil berikke yn presyzje, effisjinsje en kosten, wêrtroch't nije vitaliteit yn 'e trochgeande groei fan' e healgeleideryndustry komt.
Ferheging fan presyzje:
Yn it stribjen nei hegere presyzje sil wafer-snijtechnology de grinzen fan besteande prosessen kontinu ferlizze. Troch de fysike en gemyske meganismen fan it snijproses djip te bestudearjen en snijparameters presys te kontrolearjen, sille finer snijresultaten berikt wurde om te foldwaan oan hieltyd kompleksere easken foar sirkwyûntwerp. Derneist sil it ûndersykjen fan nije materialen en snijmetoaden de opbringst en kwaliteit signifikant ferbetterje.
Ferbetterjen fan effisjinsje:
Nije apparatuer foar it snijen fan wafers sil him rjochtsje op tûk en automatisearre ûntwerp. De ynfiering fan avansearre kontrôlesystemen en algoritmen sil apparatuer yn steat stelle om snijparameters automatysk oan te passen oan ferskate materialen en ûntwerpeasken, wêrtroch de produksjeeffisjinsje signifikant ferbettere wurdt. Ynnovaasjes lykas technology foar it snijen fan meardere wafers en systemen foar rappe blêdferfanging sille in krúsjale rol spylje by it ferbetterjen fan de effisjinsje.
Kosten ferminderje:
Kosten ferminderje is in wichtige rjochting foar de ûntwikkeling fan wafer-snijtechnology. As nije materialen en snijmetoaden ûntwikkele wurde, wurdt ferwachte dat apparatuerkosten en ûnderhâldskosten effektyf kontroleare wurde. Derneist sil it optimalisearjen fan produksjeprosessen en it ferminderjen fan skrootsifers ôffal fierder ferminderje tidens de produksje, wat liedt ta in fermindering fan 'e totale produksjekosten.
Smart Manufacturing en IoT:
De yntegraasje fan tûke produksje en it Ynternet fan Dingen (IoT) technologyen sil transformative feroarings bringe yn wafer-snijtechnology. Troch ynterkonnektiviteit en gegevensdieling tusken apparaten kin elke stap fan it produksjeproses yn realtime wurde kontroleare en optimalisearre. Dit ferbetteret net allinich de produksjeeffisjinsje en produktkwaliteit, mar biedt bedriuwen ek krektere merkprognosen en stipe foar beslútfoarming.
Yn 'e takomst sil wafer-snijtechnology opmerklike foarútgong meitsje yn presyzje, effisjinsje en kosten. Dizze foarútgong sil de trochgeande ûntwikkeling fan 'e healgeleideryndustry oandriuwe en mear technologyske ynnovaasjes en gemakken bringe foar de minsklike maatskippij.
Pleatsingstiid: 19 novimber 2024